Featured Articles
2024-08-30
[2024-08-30 ~
]
Lithium Battery Energy Storage Stations Need Hydrogen Sensors to Pre-warn of Thermal Runaway
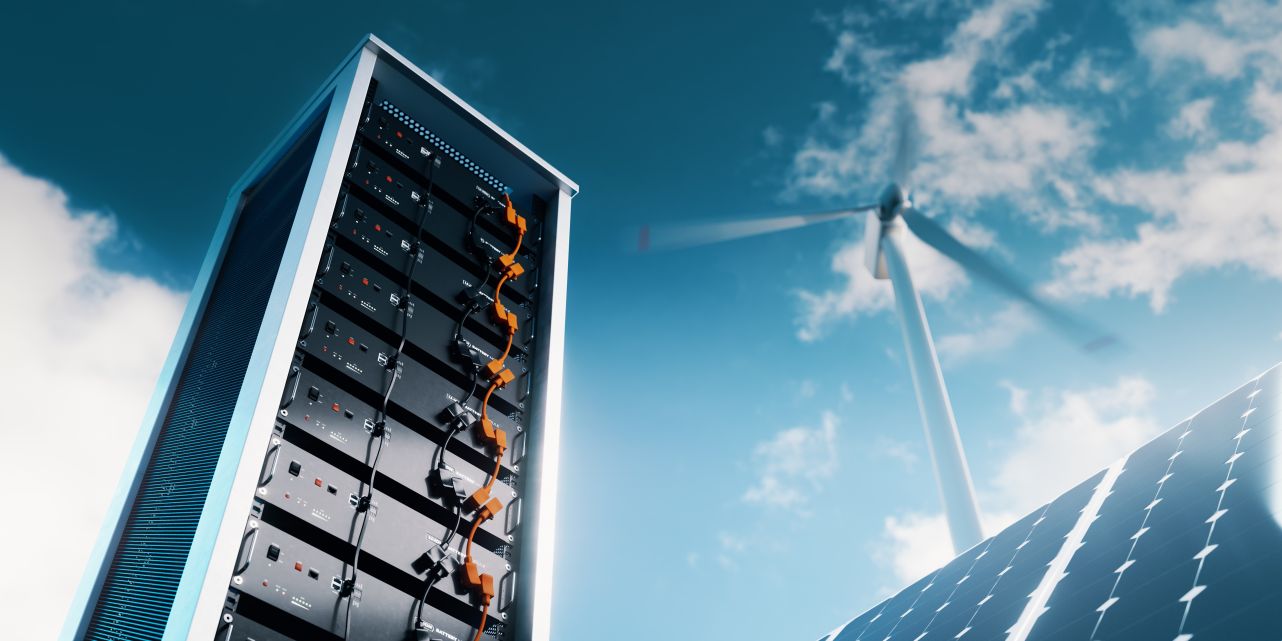
In recent years, with the popularity of wind and solar power generation, the demand for energy storage stations using lithium batteries has grown significantly in order to meet the energy storage needs of power regulation or to consider environmental factors and the necessity of replacing polluting lead-acid batteries. However, the situation of lithium batteries is different from that of lead-acid batteries. Since lithium batteries are not water-electrolyte batteries, they are sealed and will not emit gas under normal conditions. However, if thermal runaway occurs, large amounts of carbon dioxide, carbon monoxide, and hydrogen will be produced. Although lithium batteries are equipped with a battery management system that can control the charging status and monitor battery parameters, they cannot control thermal runaway events caused by internal short circuits. In the automotive industry, sensor systems for detecting thermal runaway have been developed for lithium vehicles. Most of them include hydrogen sensors and are integrated with other gas or pressure sensors.
In the past, energy storage station explosions have occurred in the United States, South Korea, the United Kingdom, Australia, China, and other places, resulting in casualties and huge losses. Furthermore, the energy storage system itself is an electrochemical reaction that is not easy to extinguish. In 2021, Tesla's energy storage system burned out for four days. Fire damage and power outages are incredibly costly, and the investment in a safety mechanism built with hydrogen sensors at its core is well worth the investment.
The Use of New Hydrogen Sensors is More Conducive to the Safe Maintenance and Management of Energy Storage Stations.
Most of the hydrogen sensors currently used in energy storage stations and charging rooms are catalytic bead sensors using the area sensing principle. The sensor consists of tiny beads coated with a catalyst such as platinum or palladium and a pair of electrodes. When gas molecules come into contact with the catalyst on the beads, they react to form new compounds. The electrode measures the heat generated by the reaction, and the concentration of the gas is determined using the principle that the heat generated is proportional to the concentration of gas molecules present. The most significant advantage of this catalytic bead sensor is that it is sensitive to various gases, and the sensor is small, can be manufactured mechanically, and is sturdy and durable. This feature is ideal for monitoring specific gases in industries such as mining, construction, and manufacturing.
However, the most significant disadvantage of the catalytic bead sensor is that it will drift over time and lose sensitivity. It needs to be calibrated every 3 to 6 months, and its lifespan is only 3 to 5 years. However, the industry's safety requirements and standards will not remain unchanged. Advanced hydrogen sensors that are more accurate and easier to manage are needed to strengthen safety mechanisms.
The microelectromechanical hydrogen sensor developed to meet the high specifications of hydrogen energy vehicles is superior to traditional catalytic bead sensors in terms of specifications, performance, and lifespan. There is no problem of calibration over time, and the lifespan can reach more than ten years. Because it adopts a semiconductor manufacturing process, it is easy to integrate with control circuits, making it easy for monitoring system manufacturers to develop systems with flexible design. The initial cost problem of microelectromechanical hydrogen sensors will be solved in the future due to the increase in demand for various applications.
Reference:
- IEEE/ASHRAE 1635-2022 IEEE/ASHRAE Guide for the Ventilation and Thermal Management of Batteries for Stationary Applications
- Power System Technology, Jeff Donato, Hydrogen Management in Battery Rooms