Featured Articles
2024-08-16
[2024-08-16 ~
]
Hydrogen Sensors Have Become an Indispensable Tool for the Safety Protection of Energy Storage Stations
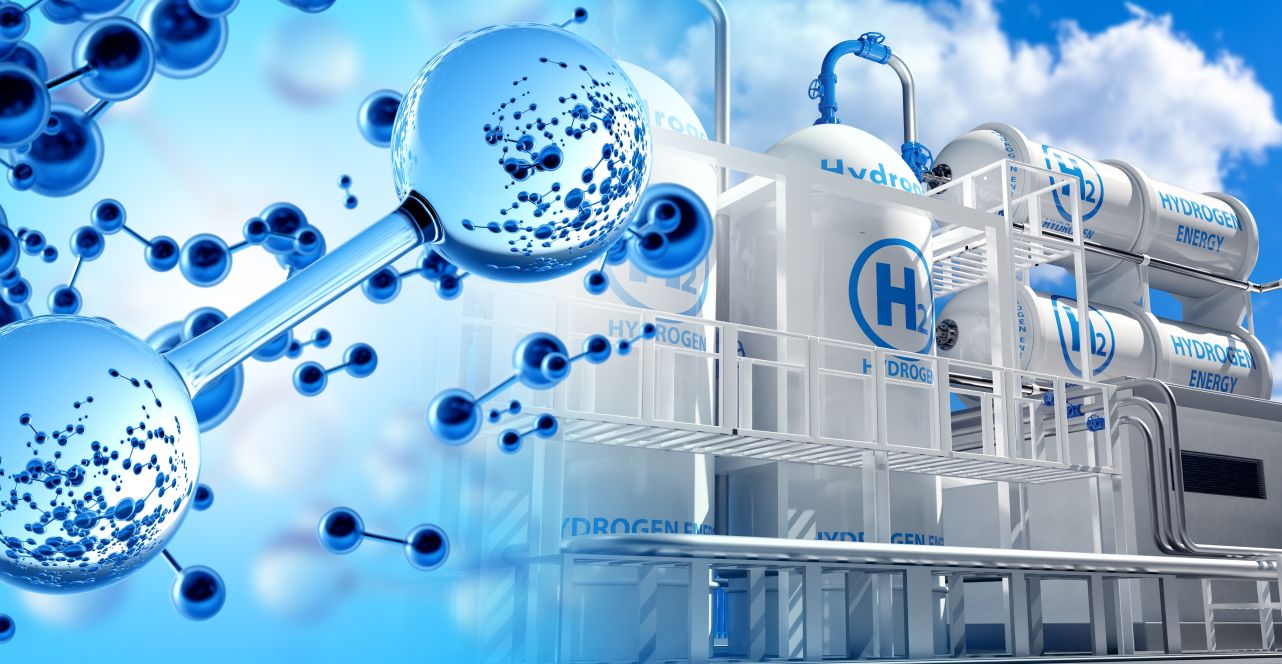
Due to convenience and cost advantages, the use of battery packs for energy storage is rapidly increasing. Commercial and industrial sites often have battery backup facilities to provide short-term back-up power in the event of a power outage. Examples include battery packs used to store energy generated from renewable sources, emergency power supplies for data centers and power for electric forklifts, among others. Warehouses, logistics centers, and many production facilities use a large number of forklifts or pallet trucks and other types of electric vehicles and, therefore, require dedicated battery charging rooms. The backup battery facilities described above often use lead-acid batteries.
Although lead-acid batteries have environmental issues, they still enjoy an advantage in price. They are commonly used in storage rooms for continuous charging, eliminating the need for expensive generators to keep the system running. However, in this kind of work using chemical energy, gas by-products will be produced during charging and discharging, which will cause safety problems in a closed space. Lead-acid batteries may produce hydrogen as a byproduct when overheated or overcharged, and their flammability is a significant concern. This is where hydrogen sensors play a crucial role in mitigating these safety risks, providing reassurance in such environments.
Lead-acid Battery Packs Have the Potential to Release Large Amounts of Hydrogen
Lead-acid batteries consist of lead oxide at the positive electrode and finely dispersed porous lead at the negative electrode, as well as an electrolyte of sulfuric acid. Hydrogen sulfide, hydrogen, and sulfur dioxide can be by-products of overcharging and battery decomposition, especially the latter two being the most common. Several conditions can occur under a variety of different conditions of use. In the event of overheating or overcharging, a small amount of hydrogen is usually produced around the lead-acid battery charge. During charging, oxygen and hydrogen are produced during electrolysis, and the amount of hydrogen produced may increase dramatically when regular charging is not possible. After heavy use or discharge, the battery is quickly restored to full load using a higher charging voltage, which produces hydrogen that is discharged into the battery storage or charging chamber.
The faster the charging speed, the higher the hydrogen production rate. When charging various types of electric transporters, such as forklifts or pallet trucks, the battery charging voltage remains high. The absorption cycle with a decreasing current can last up to 8 hours. At the end of this absorption cycle, the hydrogen is released. Depending on the power of the device, battery, and charger, as well as the charging environment, this process can produce dangerous hydrogen concentrations in the charging chamber. The extent to which a hazardous situation occurs may depend on the number of batteries, the charging rate, the size of the confined space, and ventilation equipment.
Reference:
- IEEE/ASHRAE 1635-2022 IEEE/ASHRAE Guide for the Ventilation and Thermal Management of Batteries for Stationary Applications
- Power System Technology, Jeff Donato, Hydrogen Management in Battery Rooms