Featured Articles
2023-07-11
[2023-07-11 ~
]
The Use of Composite Materials Achievable for Low Temperature and High-Pressure Storage Requirements, but the Cost too High
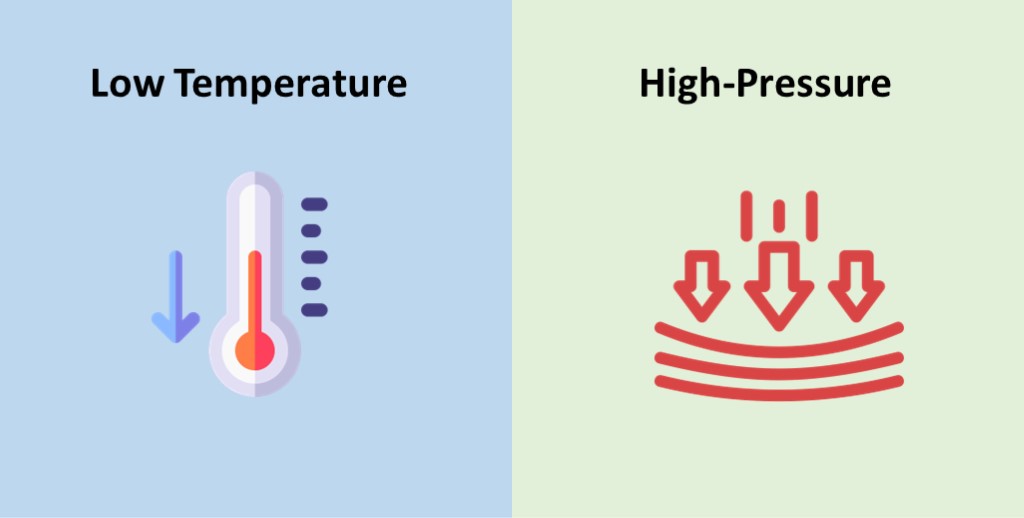
To efficiently store hydrogen, the most direct method is to change the external physical conditions of hydrogen, such as lowering the temperature or increasing the pressure. Storing hydrogen as a gas usually requires high-pressure tanks at 350–700 bar; since hydrogen has a boiling point of -252.8°C in one atmosphere, hydrogen can be stored as a liquid at low temperatures. Hydrogen can also be stored on the surface of solids by adsorption, or in the interior of solids by absorption. Therefore, an important topic for hydrogen energy will focus on the development of cost-effective hydrogen, as well as high-pressure compression storage and new material technologies that can improve energy density, so that sufficient amounts of hydrogen can be stored without sacrificing passenger and cargo space.
In the past, Type I hydrogen storage tanks almost accounted for more than 90% of the market share. However, with Type III and Type IV hydrogen storage tanks using composite materials to reduce weight and improve the efficiency of compressed gas storage due to the dual effects, the sales volume has risen sharply, and it has become the focus of market attention, especially Type IV, the highest entry barrier.
According to the American Society of Mechanical Engineers ASMC hydrogen storage tank standards, the first generation of hydrogen vehicles uses Type IV tanks, with a maximum pressure of 700 Bar, plastic lining, wrapped by expensive carbon fiber, and composite materials with sufficient strength. The advantage of using carbon fiber composite materials is that they can significantly reduce weight, which is better than all metal pressure vessels. The disadvantage is that the cost of carbon fiber is extremely high. Carbon fiber epoxy pressure vessels are produced using wet-air or tow-dipped filament winding methods, which are easier to automate and thus increase productivity. However, the required carbon fiber is relatively expensive, and the current market demand cannot reach the production scale.
It turns out that a carbon fiber production line requires an investment of about US$100 million and two years to build, which is a capital-intensive industry. Carbon fiber producers are rashly reluctant to invest in new capacity amid uncertain market conditions. In the past, hydrogen energy did not show strong demand in the market, which made the supplier's attitude quite conservative. Recently, as the trend of hydrogen energy has become more and more obvious, manufacturers of hydrogen storage tanks are quite active in expanding their production capacity, and this phenomenon is gradually improving.
Reference:
Hydrogen Fuel News, 2022-06-10, Tamy Hood, Toyota subsidiary Woven Planet creates exchangeable hydrogen cartridge
Auto evolution, 2022-05-13, Gustavo Henrique Ruffo, NamX HUV Proposes Swappable Hydrogen Capsules to Make FCEVs Practical
Hydrogen Center, 2021-09-09, Plastic Omnium wins a Major Contract With Hyundai to Supply High-end Hydrogen Vessels
Transmission Time, 2023-03-13, Kihoon Kim, Iljin Hysolus CEO "Hydrogen is not dangerous... Ultra-high pressure tank competitiveness"
日経クロステック/日経Automotive 久米秀尚, 2022-08-10, 3本合計110kgで距離30%延長 トヨタ「ミライ」の水素タンク
日経 XTECH 2015-06-25伊東敏夫トヨタのFCV「ミライ」、高圧水素タンクの炭素繊維4割削減
ASIAE, 2022-04-18, Kwak Min-Jae, Hydrogen tank technology ahead of Toyota..."If we cross the threshold, we will surpass electric vehicles"
Kurdo, 2021-11-08, Iljin Hisolus supplies hydrogen tanks to BMW following Hyundai Motors
Seoul Financial, 2022-09-22, Jin Wook Kwon, Iljin Hysolus participates in 'H2 MEET 2022' ... Hydrogen tank with stability and performance
Entreprises, 2023-05-30, Victor Cazale, Plastic Omnium, futur géant de l’hydrogène ?